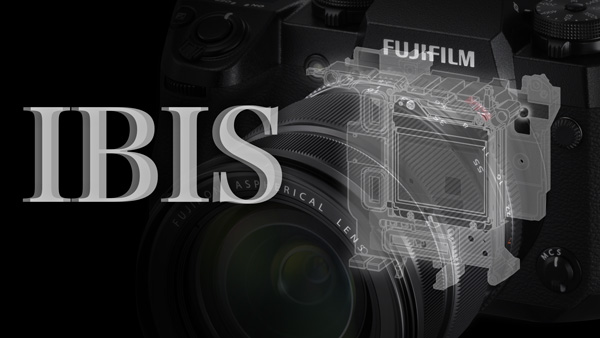
Histoire du développement du X-H1 #7
Nous avons dit par le passé qu’il n’y aurait pas d’IBIS pour la monture X. Nous l’avons dit parce que le fait d’avoir l’IBIS impliquait alors de faire des compromis sur la qualité de l’image. Mais à présent, nous devons revenir sur cette déclaration. Le X-H1 bénéficie de l’IBIS. Nous avons réussi à en développer un sans compromis sur la qualité de l’image.
Qu’est-ce qui permet une bonne stabilisation IBIS ? La précision est la clé d’une bonne stabilisation IBIS. La profondeur de champ varie en fonction de la longueur focale mais, généralement, elle est inférieure à 5 microns pour les rayons lumineux à F1.4. L’image peut devenir floue lorsqu’elle est déplacée d’un seul micron. Les objectifs XF bénéficient de caractéristiques telles que la séparation nette entre le plan focal et la zone de défocalisation. Les objectifs XF ne pourront donc pas offrir leurs meilleures performances optiques si le plan focal est incliné, même très légèrement. Une grande précision est nécessaire pour fournir le meilleur résultat.
Dès lors, comment peut-on atteindre cette précision ? Cet article va fournir des explications relatives à la conception et à la fabrication.
Tout d’abord, la conception. L’IBIS peut se décomposer en 3 grandes parties : la base, le joint et la partie capteur avec ressort.
Le secret de la base est sa fiabilité et sa solidité, comme mentionné précédemment dans l’histoire suivante :
Histoire du développement #2
Mais il y a mieux ! Le joint, en forme de bille, est placé sur la surface de la base. Pour que la bille se déplace facilement, la surface de la base doit également être lisse. Toutefois, le problème est que la plaque de la base est faite d’alliage de magnésium et qu’elle n’est pas suffisamment lisse, même une fois polie. Pour résoudre le problème, nous l’avons combinée avec une plaque en acier inoxydable à finition miroir.
La plaque en acier inoxydable a une valeur de rugosité de 0,05 Ra. Ra est la mesure de la rugosité, ce qui signifie que l’irrégularité moyenne de la surface est maintenue en deçà de 0,05 micron.
Le joint est également spécifique. Il est fait de céramique durable résistant à toute déformation. Le diamètre de la bille est de 1 500 microns et la tolérance de fabrication est de ± 0,3% (moins de 5 microns).
Et le positionnement de la surface du capteur. La surface du capteur doit s’ajuster rapidement et avec précision. La clé d’un positionnement rapide et précis est le couple. Si le moteur manque de puissance, il pourra probablement réajuster la position du capteur. Mais il ne peut pas garantir un positionnement rapide et précis.
Le moteur de l’IBIS du X-H1 est relativement grand. Il est le double de la taille d’une unité standard de capteur APS. Cela signifie qu’il est deux fois plus puissant.
Au cours du développement, l’équipe a accidentellement réglé la vitesse du générateur de vibrations au double de ce qu’elle aurait dû être. Tous les modèles d’appareils photo ont échoué au test et n’ont pas pu annuler le flou, à l’exception du X-H1. Le X-H1 pouvait encore supprimer le flou. Il est peu probable qu’une vibration d’une telle fréquence se produise dans la réalité, mais l’accident a rassuré l’équipe : un couple plus élevé a l’avantage d’augmenter la performance de l’IBIS.
Enfin, la précision est finalisée en phase de fabrication. Il serait inutile d’avoir un design et des pièces qui ne pourraient être réalisées pour la production.
La précision est atteinte avec un rapport de 1 micron. Regardez la vidéo ci-dessous pour découvrir comment fonctionne l’IBIS.
X-H1 with In-Body Stabilization (IBIS)