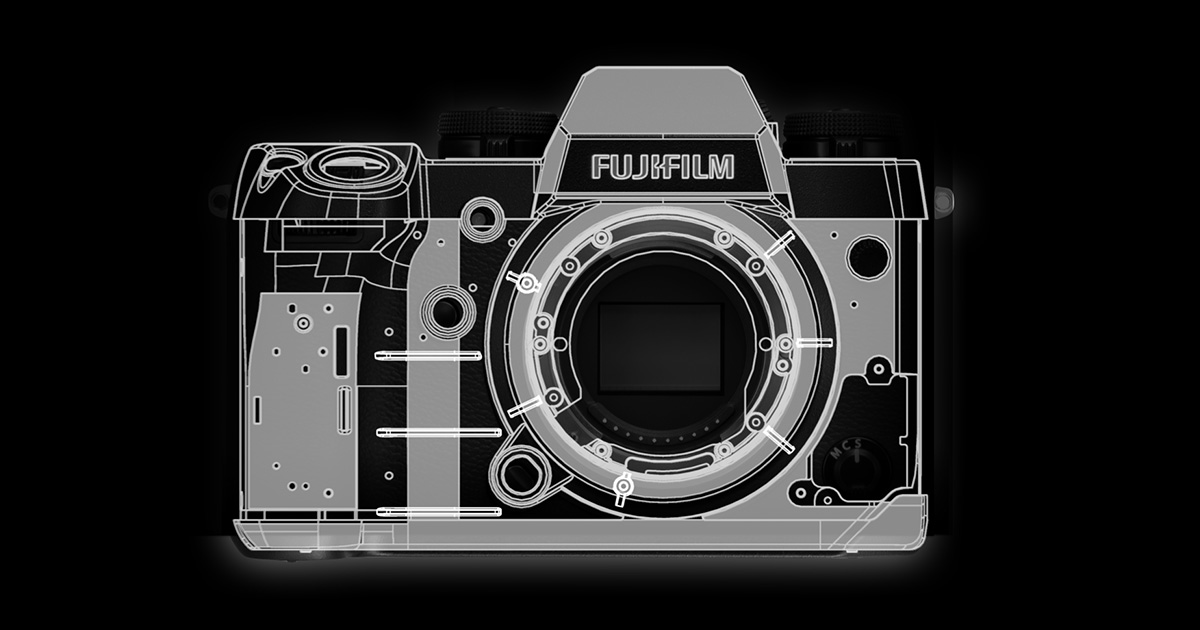
X-H1 Development Story #1
“Professional use” sounds very attractive, not only for the users, but also for the manufacturer. We can even say that this is what product planners like to think about most of the time. Why? because most items on the agenda get a pass, even if they appear unreasonable or irrational. We must try our best to meet the demand of the professionals. Developers, who have been put with the unreasonable or irrational demand, look surprised. But they don’t look puzzled, because they, too, love to take the challenge that they face.
In the series of articles, we will explore the development of X-H1 and learn how the camera evolved. Let’s begin with the story on the frame of the camera.
Recently, when a new model is announced, the spotlight is usually on devices such as sensors and IBIS units. Not much of attention is given on the exterior and body design. It seems as if the camera is weather resistant, then that is all we need to know about.
However, from the camera designer’s point of view, the exterior design is far more crucial than devices to realize a camera for professional use. When we say exterior design, we also mean body construction and framework. Unless the camera frame is durable and robust, none of the new devices could be put onto the camera.
Let’s examine the X-H1. The product planner requested the developers to make the body more robust so that new devices could be installed and the expected camera performance could be realized. In order to make the body more robust, the frame, which is made of magnesium alloys, needed to be strengthened by adding extra thickness.
The frame is 125% thicker for X-H1, meaning that the frame has almost doubled in volume (1.25 x 1.25 x 1.25 = 1.95). The strength of the frame is almost twice as strong.
Portability and lightweight are the charm of the X Series. This should always be taken into account even when considering an exterior design that is more robust. The designer examined the frame closely and learned where the stress is most/least applied and where the extra strength is most/least needed. With the study, the following structure with pillars jointing the exterior part has been realized, which helped minimize the effect on body size.
The development continued. There are certain parts of camera body that needed extra consideration. For example, front body important in terms of ergonomics and operability, but the impact on weight is huge if the entire front body were simply 125% thicker. Another extra consideration was given to the mount. In near future there will be lenses that weigh more than 2kg.
Considerable load would be applied to the mount. The mount needs to withstand the weight of the lens. Photographers move around when they are at work, so additional stress would be applied on top of the lens weight. To withstand the stress, the mount part is reinforced ribs as shown below. The mount itself is thickened and the ribs gives additional support.
This covers the basics of the exterior design.
In the next story, we will take a closer look at inside of the camera. Å
X-H1 Development Story
#1 Frame Pt.1
#2 Frame Pt.2
#3 Camera Body
#4 ETERNA
#5 ETERNA Pt.2
#6 Autofocus
#7 IBIS